Forklifts and Security - How to Reduce Accident Risks?
Week after week, countless hours are devoted to our work. As the number of hours increases, so does the risk of errors, fatigue, and stress. No one is exempt from causing or being the victim of an incident. Jobs involving handling and manual work are particularly at risk. One of the most accident-prone jobs in the logistics, warehousing and distribution industry is forklift operator. Loss of control, overturning of the forklift, flat or under-inflated tires directly impact the safety of people and equipment. Often overlooked, the choice of tires also has a direct influence on performance and safety. To prevent and identify signs of wear, it is crucial to inspect the tires on your machines regularly.
To limit incidents and make the workplace enjoyable and safe, factories and shops around the world are implementing policies and actions to protect their employees. By giving proper instructions and training to workers, by assessing avoidable risks and considering the limits of the equipment used, we can reduce the potential for incidents. Let's take a look at the most common causes of forklift accidents, how can they be avoided and what tires have to do with it.
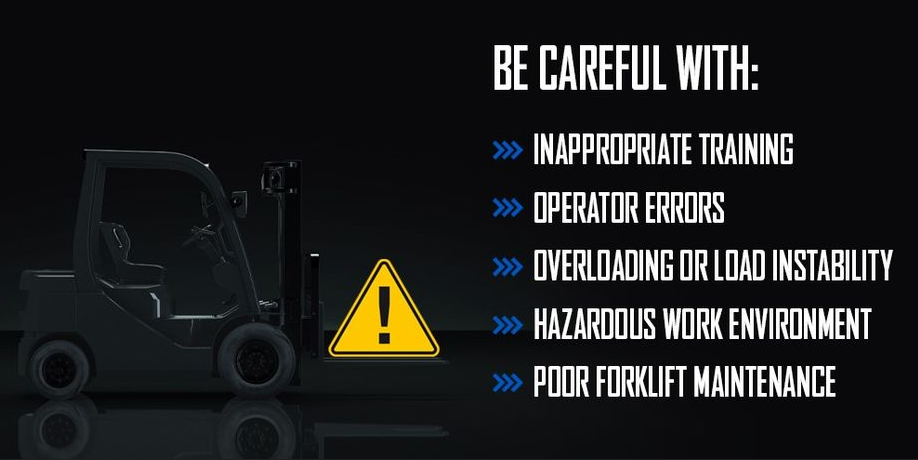
What causes forklift accidents and how can they be avoided?
1. Inappropriate training
Many forklift-related incidents could be avoided with proper training. Education on security procedures, emergency protocols, specificities of work environment, equipment, and maneuvers is crucial to ensure safe work environments. Most manufacturers offer complete forklift training for operators. It is also possible to get information from local organizations and companies.
2. Operator Errors
To err is human. Sometimes the lack of information is to blame, sometimes it is the lack of judgment. Excessive speed, abrupt driving and moving around with the load lifted are high-risk behaviors that must be avoided. Setting up systems and work methods, and encouraging communication between workers, can help keep operations running smoothly.
3. Overloading or load instability
An unbalanced load can cause instability and lead to an overturn of the forklift. It is one of the most dangerous incidents. This could result in major injuries to the driver or people in the environment. The products must be stacked with care and be stable. Each type of forklift has its load capacity, it is always wise to respect it. The information is usually marked on the vehicle. In addition, overloading the vehicle can have an impact on tire performance: excessive heat build-up, reduced operating speeds and premature wear are examples of the consequences of overloading.
4. Hazardous work environment
A work environment with slippery surfaces and misplaced objects (shelves, electrical dangers, walls, other vehicles) can increase the risk of accidents. Reckless driving, inadequate traffic management and insufficient lighting are just a few examples. Maintaining a clean, organized environment and using the right protective equipment can help reduce the number of accidents.
5. Poor forklift maintenance
Forklifts require regular maintenance to keep them running safely and avoid mechanical, electrical, or hydraulic problems. Here is a short checklist of items to verify when you perform routine inspections on your forklift:
- Check all tires for damage and good service
- Check tire inflation pressure (pneumatics)
- Make sure wheels are torqued correctly
- Make sure all controls are functioning properly
- Check hoses and lines for leaks
- Inspect fork for damage and heel wear
- Check brakes
What does security have to do with tires?
What bonds tires, operator and equipment is stability. Tires that show signs of fatigue without being replaced can lead to a risk of tipping, skidding or loss of control. Traction will also be reduced.
Diverse types of tires can be installed on forklifts. The right tire must be chosen to suit the intensity level and the specific work environment in which it will be used. The right tire for your application can avoid many security concerns and reduce your maintenance costs.
Here are the basics to know to make a more conscious choice:
- PON (PRESS ON TIRES) Technology. A good option for operations involving short distances with heavy loads, with or without irregular ground surfaces. It also offers high stability, crucial for safety, and enhanced braking capacity.
- RES (RESILIENT) Technology. A tire that offers enhanced driver comfort and extended service life. It is also puncture-resistant, reducing downtime and maintenance costs.
- BIAS Technology. An advantageous choice for intensive, heavy-duty applications. This type of tire offers good stability on uneven surfaces and good traction at low speeds.
To find out more about the signs of wear associated with each tire technology, watch our educational videos. Our Usage Intensity Calculator is also available to help you choose the right tire according to your application. Don't hesitate to call Solideal On-Site Service for more guidance and professional advice. You can also click here to find a dealer near you.
Implementing security rules and standards can help reduce incidents related to equipment, environment, human resources, management, or task type. For forklift operators safety, training and accredited certification can make all the difference in preventing accidents. Let's not forget that good equipment maintenance and compliance with maximum loads enable the operator to maneuver the vehicle better and be more stable. Well-maintained tires provide better traction and performance. Small preventive measures can save costs, time, and unfortunate incidents. Be careful of yourself and others!